As the mining industry delves deeper for resources, microchip design principles could deliver mapping techniques that keep expensive access tunnels to a minimum.
According to researchers at University of Melbourne, two seemingly unrelated design disciplines – mining and microchips – actually have much in common.
Professor Doreen Thomas and Professor Hyam Rubinstein have applied their knowledge of network optimisation techniques for microchips to the mining industry. They’ve created software for designing and planning complex underground tunnel networks.
“When designing microchips, you have wiring that needs to link up multiple nodes on the chip. There are thousands of nodes that need to connect together and you want the wiring to be as short as possible so that you have the least number of faults, allowing the electronics to be as fast as possible,” Thomas said.
She compared this to planning mine access tunnels, which follow the same general rules. Access tunnels are a huge financial burden on a mine, and optimal tunnel mapping could determine the feasibility of a mining project.
“If our software can shave a few percent off the length of the tunnels, it can save millions of dollars over the life of the mine,” Thomas said
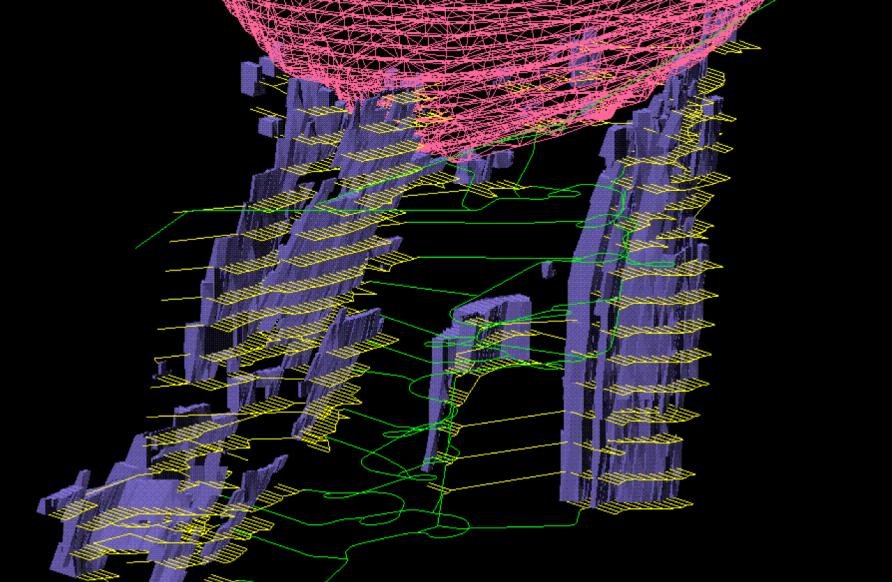
Global professional services company EY reports that accurate cost and schedule control is crucial to mining and metals projects, and that ill-defined scope and execution of engineering and project controls have led to the need to defer or cancel projects, or absorb the resulting costs.
“With the huge expenditure on current projects, schedule delays or cost increases – when coupled with fluctuating commodity prices – are now materially impacting the financial performance of organisations involved in their execution,” said EY advisor Claus Jensen.
Underground understanding
Mine tunnel networks are complex and can run up to 30 km beneath the ground. According to Rubinstein, a major challenge for the mining industry is the need to tunnel further underground as surface deposits are depleted. This begs the question: “How do you mine safely and economically at depth?” he asked.
“Deeper mining will require more automation for safety and to cope with higher temperatures and ventilation requirements. Our access network optimisation research and software gives mining companies important tools to tackle these challenging tasks,” Rubinstein said.
According to Thomas, one advantage of efficient mapping using their software is the ability to plan tunnels in such a way as to allow as much earth and rock as possible to remain underground, reducing the costs of removal.
The software will also allow much more efficient design processes than are currently possible.
“The idea with our software is that it allows you to create 200 access network designs in two weeks instead of two designs in six months,” Thomas said.
And the potential of this software has not gone unnoticed by the global mining industry. MineOptima, the startup founded by Thomas and Rubinstein to commercialise their software, was acquired by international mining software and consulting company RPM Global in August 2017.
Richard Mathews, CEO and managing director of RPM, said in a media release that the strategic acquisition of MineOptima would fast-track RPM’s underground mining solutions through industry-leading tools.
“The MineOptima products minimise development and haulage costs and deliver users a 3D rendering of an optimal decline network for their underground mine,” he explained.
Mathews also cited the software’s ability to take into account operational constraints, as well as its ability to determine optimal locations for breakouts of subsidiary declines in the network.