How did a materials-handling engineer get asked to design stadium roofs and ferry wharves? By keeping his eye on the ball and recognising opportunities to pursue innovative design.
Back in the 1990s when Connell Wagner (one of Aurecon’s forerunners) pitched for the job on the roof at Docklands Stadium in Melbourne, the team there had no experience in this area to bring the innovative design to life.
Luckily, it had a mechanical engineer in Queensland who had done a lot of work on large stockyard machines weighing 1000 t, which arguably have greater design challenges than those facing the roof at Docklands.
“We put the case that it was actually less complex than these big, moving, materials handling machines that we had done a lot of,” said that engineer, John Leech.
When Connell Wagner won that contract, Leech had to become an expert in retractable roofs quickly, exploring state-of-the-art solutions overseas. But he says the solution proposed was different to anything else being done at that time.
“It spans the length of the field, 165 metres, so it’s a massive span, and the whole problem was, what happens if one side stops for some reason, and the other side keeps driving? You can generate massive loads,” he said.
“A lot of the other systems that we looked at actually relied on the control systems and on the flexibility of the roof, so that you could get away with a fair bit of movement. We weren’t happy to go that way on that system, so we ended up articulating it about a virtual pivot using hydraulic balancing. You can drive it into skew if you want to, without generating any bad loads, but of course under normal operation, keep it in motion. Then if one side does stop, you have time to detect it going into skew.”
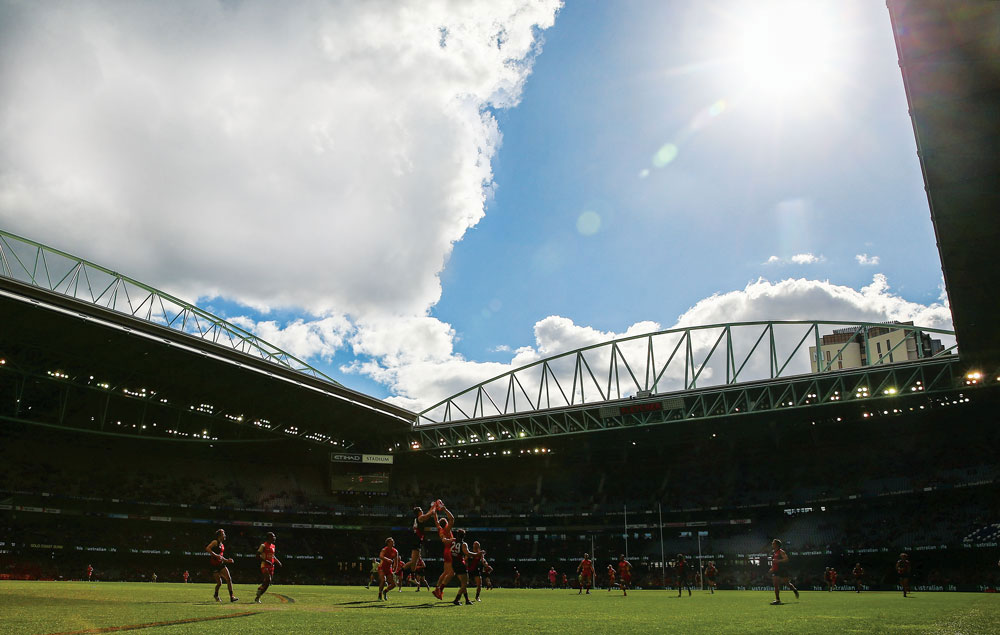
Now, when Aurecon pitches for jobs like redesigning the retractable roof on the Rod Laver Arena in Melbourne (which they won), it can point to a lot of experience in this field both in Australia and overseas.
The same design principles from the Docklands work will apply on the roof upgrade job at Rod Laver Arena, which won’t be finished until after the 2018 Australian Open.
“We’re following the same philosophy as we used on the previous roofs in terms of allowing them to articulate freely without any destructive loads coming into place,” he said.
“What’s new is the detail of how we’ve compacted all of that in the space that we had to play with. Because it’s a brown-field site, we’re restricted to having the new bogeys fit the same space as the old bogeys, and to apply the loads to the fixed roof structure at the same span as on the existing.”
He explained that, because it was the first moving roof in Australia, it was built using state-of-the-art technology for the time, but it was very slow. It takes 25 minutes to go from fully open to fully closed. For contrast, Margaret Court Arena takes just four minutes.
The conveyor belt
Born and raised in Brisbane, Leech had no engineering role models as such and wasn’t even really sure what engineers did, but his teachers and his parents all seemed convinced it was the ideal career for him.
“I think that’s the case with most students who go into engineering,” he said.
“They know they like structures or mechanical things, from all of the products that they come in contact with through their lives, Lego, Meccano, that sort of thing. I think they get an inkling that they have a leaning towards that, but I don’t think many students really understand what engineers do when they go into it. I certainly didn’t. It was only when I started work experience that I really saw what they did. Fortunately, it was what I wanted to do.”
That work experience was with Macdonald Wagner and Priddle (MWP, a forerunner of Connell Wagner and Aurecon) at the Dalrymple Bay Coal Terminal (DBCT) near Mackay in northern Queensland.
Following graduation, MWP welcomed him back as a permanent engineer and he began to specialise in materials handling. He said this was a valuable learning experience where he began to apply the skills he had learned at university.
“In bulk materials handling, you’re often working on big projects, so when you come in as a graduate, a senior engineer has usually worked out what needs to be done, in terms of the type of equipment, its handling rates, speed, control requirements,” he said.
“Then you’re just focused on the detail, like if we want a conveyor from here to here, it’s got to do this rate, and you go into the detail from there.”
Although he was going by the book at this stage of his career, Leech was also watching how the more senior engineers approached their tasks. He realised that to be successful, he had to be more creative in his solutions.
Innovative design thinking
Leech said he was inspired by an engineer called Alan Huth at the RG Tanna Coal Terminal in Gladstone, who had developed a retractable tripper to divert material on the conveyors when needed. At DBCT, Leech needed to take a diversion off a conveyor partway through the process. He knew he needed something like Huth’s tripper but different because Huth’s solution wouldn’t work in that situation.
“It was the way we actuated it, that I think was the difference,” he said.
“We put the cylinders in tension instead of using a rotary drive so it handled the higher loads better. We also put extra segments onto it, so that it was a lot softer curve.”
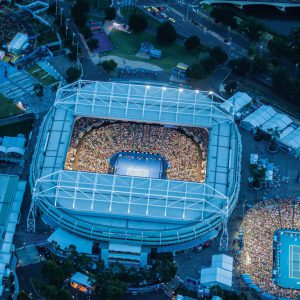
Leech said engineers do incremental innovation all the time, often just small changes to make something operate smoother or faster – but it’s still innovation.
“You’ll normally do some sort of incremental innovation because it’s safe. You can usually predict the outcome, you know it’s going to be better than what was done before, and you’re normally not bringing in any new risks,” he said.
“It’s when you have no choice but to come up with something different in order to solve a problem, that you are more likely to go for that really different innovative approach. There’s no better source of innovation than when you’ve got a challenge that can only be met by an innovative solution.”
He gave an example of another tripper they began developing at Dalrymple Bay.
“We had to put a tripper into an existing set of in-loading conveyors at DBCT,” he said.
“If we’d done it in a traditional way, put a traditional tripper in, or even one of our pop-up trippers in that we’d developed to a fairly finessed point by that time, there was going to be huge costs involved, and huge downtime.”
Leech and his team realised they could reduce both the cost and downtime substantially by pushing the belt down instead of lifting it up to create the drop point.
“This was an idea that would have allowed us to do all of that work within two trestles. We didn’t have to touch the rest of the conveyor,” he said.
“It could all be constructed above the belt, prior to the shutdown. A little bit of work underneath, had to be done during the shutdown, but it was going to greatly reduce the shutdown, and overall costs.”
Encouraging innovation
These days, Leech is a design director at Aurecon, a role he said has been created for projects that have an especially challenging technical aspect to them so the design director can oversee the technical output and help foster innovative thinking. The job, he feels, best exemplifies this approach is the redesign of the Brisbane ferry terminals.
The problem was, in the 2011 floods, the river reached a level where the gangway tether point was under water so the gangways were also under water, making them vulnerable to debris floating down the river. This contributed to the failure of a number of wharves during those floods.
“They wanted us to come up with a solution that was resilient, that they could put back into action quickly after the floodwaters had receded,” Leech said.
“The key part of the solution is that the gangway has a flotation chamber underneath that develops buoyancy as the water rises. As you get to a certain water level, which is well above the normal high tide operating level, where the abutment is running with water by about 600 or 700 mm deep, so no one’s going to be using it, then it releases at the end and the gangway swings around.”
Leech says the process for coming up with the design was very much a team effort.
“We used a lot of paper, a lot of hand sketches,” he says. “There’s something about the whole process of sketching and thinking. The sketching feeds back on your thoughts and vice versa, and it all just sort of comes together.”
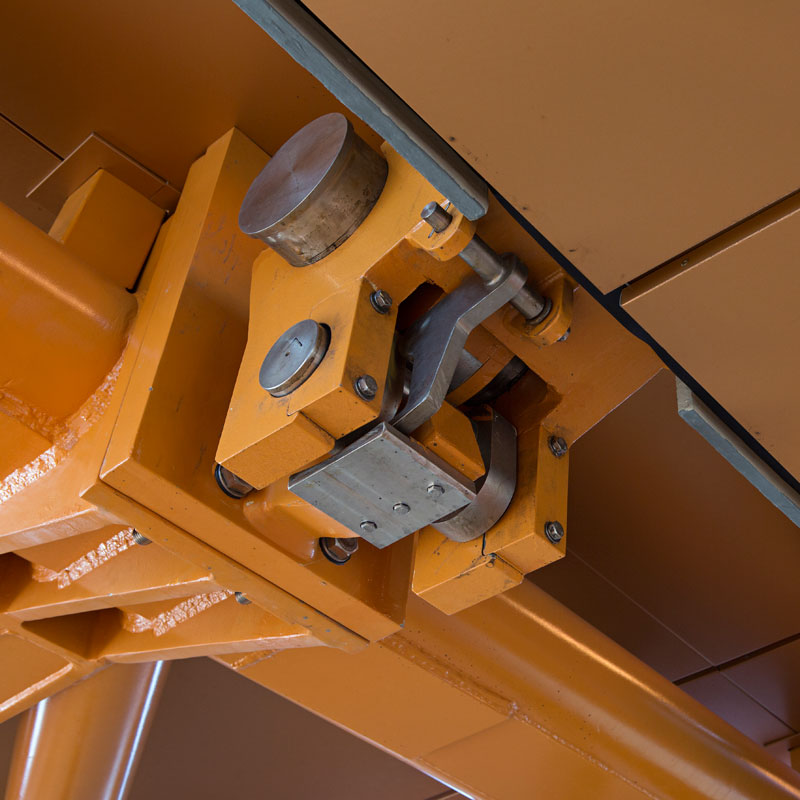
He believes the key to coming up with an innovative solution is for the whole group to understand the problem.
“To get behind the immediate problem or thing that they might be trying to design, you need to really understand what is it about the client’s production method, or their materials handling, supply chain, or in the case of the ferries, what is it we’re actually trying to do,” he said.
“Make sure everyone understands that, that really fundamental need, and then there’s more of an environment there for everybody on the team to have ideas about what might work. It’s not necessarily from the mechanical person, you might get it from, the electrical person.”
He also believes engineers should be trying to think innovatively from the moment they join the company, even if they’re new graduates. “I think it’s just getting them to question whether it is the right solution, and literally asking them, ‘What is the problem we’re really trying to solve? That is a good way of doing it, but is there another way?’,” he said.
“In practice, it would happen more often when the senior engineer supervising, perhaps sees there’s an opportunity there to do something, and often you would actually try and not mention exactly what it is that they’re thinking at the time, but just asking them, ‘Do you think there’s another way of doing it? Because if we do it this way, it’s going to cost this much, and we’re going to have these problems’.”
Waiting for rain
Leech believes part of the reason engineers aren’t more highly regarded in the wider community is they design things so people don’t even realise they’re doing the job.
“Lay people are used to having products all around them that just work,” he said.
“They don’t often appreciate what’s gone on behind that. If there’s something new and unique, they won’t understand the depth of thinking and the time and effort that went into getting it to that point.”
He said Aurecon recently set up an academy to help teach its engineers to communicate ideas better to clients and the general community, a subtle skillset not unlike a language translator, involving listening and explaining without using foreign terms.
“There’s a big section on storytelling,” he said.
“And there’s lots of good stories in all of our engineering projects. But often we don’t tell them that well. We tend to skip to that technical side, and don’t break it down to what we did for society, what the basic benefits of it were, and talk about the challenges in a way that the layperson can understand.”
That said, there will always be innovations that only engineers ever truly appreciate. When the upgraded roof at Rod Laver Arena is finished, Leech will be hoping it rains just to see it close.
“Most of the public will just go, ‘Oh, yeah, the roof’s closing. I’m going to get a bag of chips’,” he said.
“But there’ll be this little proportion of people in there, probably the engineers, who go, ‘Wow, look at that! I wish I could see that better’.”